THE FUTURE OF TEXTILE MANUFACTURING

Hemp as an Alternative Textile
Hemp is a natural fiber that is stronger and more durable than cotton and provides better ultraviolet (UV) protection than other natural fiber-based fabrics like cotton.
The Farm Bill effectively removed industrial hemp from inclusion in the Controlled Substances Act (CSA) and became legal in the U.S. in 2018.
Extremely sustainable, hemp requires minimal water and pesticide use in its cultivation. Hemp is also biodegradable and returns some nutrients to the soil.
Hemp is naturally hypoallergenic, antiviral, antibacterial and antimicrobial. This is beneficial to farmers because hemp can be grown in a more eco-friendly environment with greatly reduced needs for fertilizers and pesticides.
Costs Production
Potential Hemp Costs
Estimated production expenses are $286, net returns of hemp for fiber ranged from -$116 to $473 per acre. Returns for hemp seed were estimated to range from $60 to $800 per acre. Given costs of production at $196 per acre, net returns ranged from -$136 to $604 per acre (McNulty).

Manufacturing Components
Hemp plant grows from seed in a variety of different soils but preforms best on land that grows corn. The soil must be non-acidic, rich in nitrogen, and well drained, as well as mild climate with a humid atmosphere, and 25-30 inches of rain.
Plant is ready for harvesting when plants begin to shed pollen. (Mid August for North America). 70-90 days after seeding.
For hemp textiles; specific cutting technique is required.
Once cut, "the stalks are allowed to rett (removal of the pectin [binder] by natural exposure to the environment) in the field for four to six weeks—depending on the weather—to loosen the fibers." (Madehow, 2021)
Hemp seeds must be properly cleaned before storing.
"To separate the woody core from the bast fiber, a sequence of rollers (breakers) or a hammermill are used. The bast fiber is then cleaned and carded to the desired core content and fineness, sometimes followed by cutting to size and baling. After cleaning and carding, secondary steps are often required. These include matting for the production of non-woven mats and fleeces, pulping (the breakdown of fiber bundles by chemical and physical methods to produce fibers for paper making), and steam explosion, a chemical removal of the natural binders to produce a weavable fiber. Complete processing lines for fiber hemp have outputs ranging from 2-8 short tons/hour (1.8-7.2 t/hr)." (Madehow, 2021)
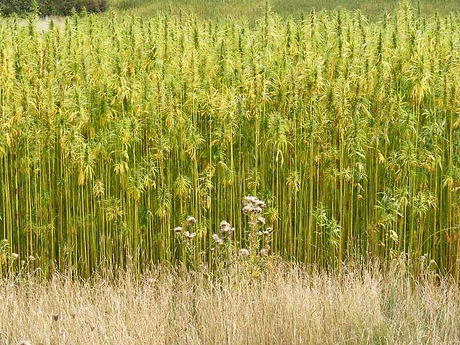
Energy
Hemp is essentially a plant that needs electricity to grow.
1kg of usable hemp fibers account for 2,041-3,401 liters of water compared to cotton that accounts for 9,788- 9,958 liters of water (Charret et al., 2005)
Hemp fiber represents a low ecological
footprint with 1.46-2.01 gha (Charret et al., 2005), world average hectare, gha.
300-500 liters of water to produce 1kg of dry hemp matter

National Hemp Association
The National Hemp Association's goal is to support the growth and development of all aspects of the industrial hemp industry by educating the public and collaborating with a community of workers, scientists, businesses, and government officials.
The NHA would have a positive outlook on the capital gains tax, since they endorse resources for passing hemp legislation. The subsidy from the tax will support hemp farmers, which qualifies as helping the development of the hemp industry as the NHA aspires to do.